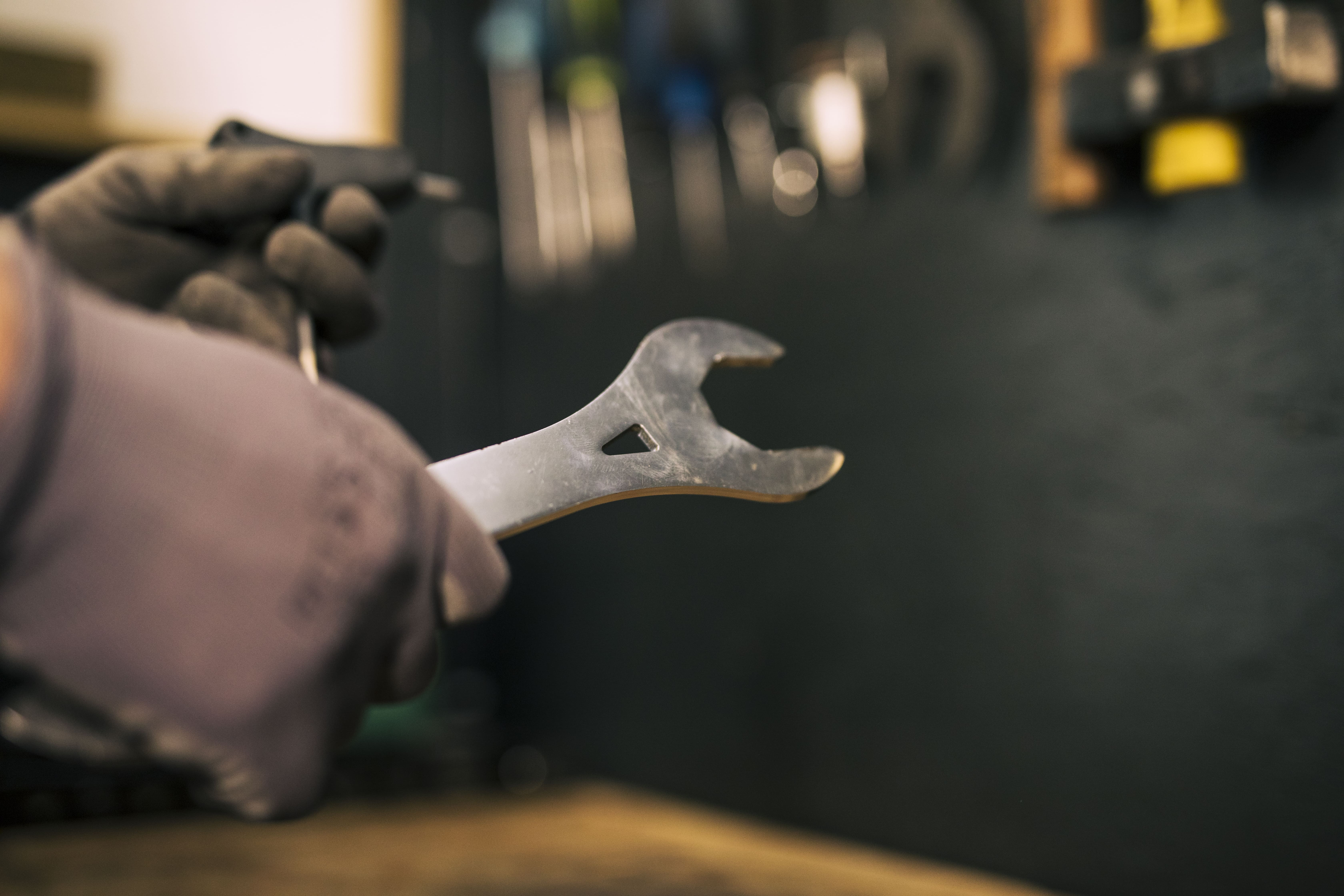
Learn about corrective maintenance and its advantages to optimise your assets
2024-09-05 07:00:00
In the day-to-day operations of any company, teams and systems work tirelessly, like essential pieces of a complex machine. However, inevitably, there comes a moment when something fails. It is in those moments, when operations stop and time is of the essence, that a crucial solution steps in: corrective maintenance.
What is corrective maintenance?
Corrective maintenance is about fixing things when they go wrong. It is the reactive side of maintenance, where we address failures, breakdowns, or malfunctions that occur unexpectedly. While preventive maintenance aims to prevent problems in the first place, corrective maintenance is our reliable backup plan when things don’t go as planned. It works reactively, as it is the part responsible for responding to breakdowns when they happen.
Corrective maintenance arrives just in time, addressing unexpected problems. It is the immediate response to failures, breakdowns, or malfunctions that appear out of nowhere. It’s like an emergency doctor diagnosing the problem and fixing it quickly and precisely.
But why is this type of maintenance so important? The answer is simple: downtime in any organization is a costly enemy. Every minute a machine is out of service is a lost minute of productivity, a minute of delay, a minute of unsatisfied customers.
Corrective maintenance is the line of defense, the guarantee that operations continue, that production doesn’t stop, and that the company's pace is not affected.
Corrective maintenance not only reacts to problems; it also learns from them. Every failure or breakdown provides valuable insights into the reliability and performance of our equipment and systems. By analyzing these events, we can identify trends, root causes, and potential areas for improvement. This knowledge can be used to adjust our preventive maintenance strategies, reducing the likelihood of similar problems in the future.
What types of corrective maintenance exist?
Corrective maintenance has many facets, each with a specific approach to addressing problems:
- Emergency corrective maintenance: This type of maintenance is carried out when a critical failure occurs that requires immediate attention. The goal of emergency corrective maintenance is to restore functionality as quickly as possible to minimize downtime and prevent further damage. It often involves deploying specialized technicians and urgently allocating necessary resources.
- Deferred corrective maintenance: Deferred corrective maintenance refers to postponing the repair or restoration of equipment to a more suitable time. This approach is typically adopted when the failure or malfunction does not immediately affect operations or safety. However, it is important to carefully assess the risks and consequences of delaying maintenance to ensure that it does not lead to more significant problems in the long term.
- Scheduled corrective maintenance: This type of corrective maintenance is more proactive. It plans and schedules repairs at strategic times, minimizing the impact on operations and ensuring that resources are used efficiently.
- Predictive corrective maintenance: Predictive corrective maintenance uses data analysis and condition monitoring techniques to anticipate and address potential failures before they occur. This approach allows proactive maintenance actions to be taken, preventing unexpected failures and reducing the need for reactive maintenance.
- Reactive corrective maintenance: This is the most traditional type. It waits for the problem to manifest before taking action. It is the immediate response to the emergency but is not always the best option.
The advantages of corrective maintenance: a strategic approach to efficiency
Corrective maintenance, although based on reacting to unexpected problems, offers several advantages that can contribute to the overall efficiency and effectiveness of maintenance operations.
What are the key benefits?
- Cost-effectiveness: By addressing breakdowns reactively, companies can avoid unnecessary preventive maintenance tasks and associated costs. Resources are allocated to areas that truly require attention, optimizing maintenance budgets.
- Minimization of downtime: Corrective maintenance seeks to minimize the time equipment is out of service. By solving problems quickly, the impact on production is reduced, interruptions are minimized, and a continuous flow of operations is maintained. This translates into greater productivity and customer satisfaction.
- Efficient resource allocation: Corrective maintenance enables efficient resource allocation, especially of specialized labor and spare parts. Maintenance personnel are deployed where their expertise is needed, and spare parts inventory is strategically managed, avoiding unnecessary stockpiles.
- Improved equipment reliability: By analyzing the causes of failures and taking corrective actions, companies gain valuable insights into the reliability of their equipment. This information is used to make informed decisions about maintenance strategies, identify areas for improvement, and adjust preventive maintenance programs, contributing to improved equipment reliability and minimizing future breakdowns.
- Learning opportunities: Every equipment failure is an opportunity to learn. Corrective maintenance allows a better understanding of equipment behavior, failure modes, and root causes. By analyzing these failures, patterns and common problems can be identified, and preventive measures can be implemented to mitigate future risks. This continuous learning process helps build a knowledge base that can be used to optimize maintenance practices.
- Flexibility: Corrective maintenance offers flexibility in maintenance operations. While preventive maintenance follows pre-established schedules, corrective maintenance allows for an adaptable response to unforeseen events. Maintenance teams can address urgent issues and allocate resources in real time, ensuring that critical failures receive immediate attention.
- Integration with predictive maintenance: Corrective maintenance can be integrated with predictive maintenance strategies, creating a comprehensive maintenance approach. Predictive maintenance technologies, such as condition monitoring sensors and data analysis, can provide early warnings of potential failures. By combining corrective maintenance with predictive insights, companies can take proactive actions, prevent breakdowns, and reduce the overall maintenance burden.
Maintenance software: a strategic ally for corrective maintenance
Maintenance software, such as Computerized Maintenance Management Systems (CMMS) or Enterprise Asset Management (EAM) systems, has become a fundamental ally for optimizing corrective maintenance activities. These digital tools offer a series of advantages that streamline the response to breakdowns, improve efficiency, and enable smarter resource management.
How does maintenance software help?
- Work order management: The software allows for quick and efficient creation, assignment, and tracking of work orders. This ensures that repairs are scheduled and assigned to the appropriate technicians, avoiding delays and improving coordination between maintenance teams.
- Asset tracking: The software centralizes information for each asset, including its maintenance history, performance metrics, and repair records. This facilitates informed decision-making and allows technicians to access relevant information to diagnose and resolve issues effectively.
- Real-time monitoring: The software can integrate with condition monitoring systems, providing real-time updates on the status of equipment. This allows anomalies to be detected and preventive measures to be taken before serious failures occur.
- Inventory management: The software facilitates precise tracking of spare parts, optimizing inventory levels and ensuring the availability of critical components when needed. This reduces downtime and costs associated with the lack of parts.
- Data analysis: The software collects and analyzes data on corrective maintenance activities, allowing for the identification of recurring issues, assessment of equipment reliability, and optimization of maintenance strategies.
- Documentation and compliance: The software helps capture and maintain digital records of maintenance activities, ensuring compliance with regulations and standards.
- Integration with other systems: The software can integrate with other enterprise systems, such as inventory management, purchasing, or financial systems, optimizing workflows and data exchange.
The key to achieving strategic success
Corrective maintenance, while a reactive approach, needs to work in conjunction with other strategies to be truly effective. The key to success lies in an integrated maintenance strategy that combines corrective, preventive, and predictive maintenance. Each type of maintenance has its role, but all work together to achieve a common goal: the safety and efficiency of the company.
Corrective maintenance, like any process, can evolve. Technology, innovation, and artificial intelligence are transforming the world of maintenance, creating new tools and strategies to prevent failures, optimize resources, and improve efficiency. In the not-too-distant future, corrective maintenance will not only be about putting out fires but will be a strategic ally that works alongside the company to ensure operations run optimally, equipment is reliable, and production is efficient.
If you want to learn more about our solutions and how we can help you transform the maintenance management of your establishment, don’t hesitate to contact us. Let's face your next challenge!